Creating Futuristic and Stylish Interiors for New Electric Vehicles
New film solves issues of design, surface hardness, and environmental load in one fell swoop.
Automobile interior manufacturer Design and development division
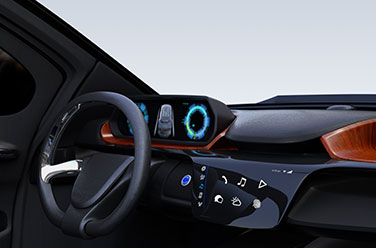
The manufacturer featured in this case study had received a request from an auto manufacturer, via a components supplier, to assist with developing the interior for a new model of electric vehicle. The auto manufacturer’s designers had expressed a strong desire that the interior be stylish, to suit the vehicle’s futuristic exterior. Meanwhile, the interior manufacturer’s purchasing division requested that the materials used be sourced in accordance with its environmentally friendly procurement policy, in order to reduce the environmental impact of the manufacturing process. The need to balance these two requirements was a headache for the design and development team.
Problem
Instead of Physical Buttons, Wish to Use Light Transmissive Indication and Electrostatic Switch
The manufacturer is supplying critical components that would be positioned in the center of the instrument panel, a place where air-conditioner controls and other buttons are grouped together. The designers had requested that the interface be more stylish than the traditional style of physical buttons and toggle switches.
In the course of gathering information on the latest solutions, a member of the design and development team decided that a light transmissive indication combined with electrostatic switch would best meet their requirements. Because the manufacturer has experience with using insert-molded printed films in their mass production, it believed it would be able to produce the required components by making the printed portions see-through, and compatible with electrostatic switch. At the prototype stage, however, it discovered an issue with film thermoforming.
Because the transparent portions of the indication (text and symbols) needed to be positioned accurately, the thermoforming film that is prepared before insert molding is carried out needs to be readily formable. However, films with hard surfaces tend to have poor thermoforming characteristics: this fact presented the greatest challenge in the course of translating the concept into reality. The purchasing division’s green procurement policy further complicated the materials selection process.
Thus, the development team was forced to come up with a brand new manufacturing process.
Summary of the Problem
- While the manufacturer wanted to combine a light transmissive indication with electrostatic switch to fulfil the designer’s request, it discovered a problem with the thermoforming films used.
- If the manufacturer used the same film thermoforming-based process that it had used in the past, it would be unable to achieve both surface hardness and thermoforming performance.
- Besides, the procurement division’s environmentally-friendly purchasing policy made the selection of materials even more difficult.
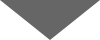