Conflicting Customers’ Requirements Make a Hurdle in Developing a Resin for Car Body Weight Reduction.
Cyclic carbodiimide makes impact and heat resistant resins possible.
Resin manufacture Research and development *This article is an image story of problem solving using our products
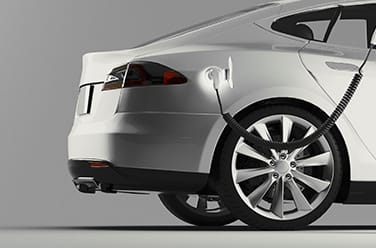
New electric vehicles are being developed and released at a brisk pace, and demand for ways to reduce vehicle weight to improve range, fuel economy, and battery life is especially pronounced. The plastics producer featured in this case study, which supplies performance plastics to order, had received an inquiry from a major automotive parts manufacturer.
Problem
Plastics Producer Faced Tradeoff: Meeting Client Requirements Would Mean Adversely Affecting Physical Properties
The manufacturer wanted to know whether it was possible to create a new type of resin that could be easily molded and had excellent fire resistance without sacrificing impact or heat resistance.
An employee from the research and development team recalls:
“The manufacturer said they wanted a material that would help reduce vehicle weight, but it is difficult to give a single resin opposing properties, like heat resistance and moldability, at the same time. Rather, to create a resin with the desired characteristics, we needed to combine various materials and fillers. An infinite number of combinations of materials and compatibilizers is possible,” says the employee.
The team decided to start by rethinking the materials and fillers used, and start work on a prototype once they had narrowed down their options somewhat. The team tried compatibilizers used in both currently and formerly produced plastics, and built and tested many prototypes, each featuring a different combination of materials and compatibilizers.
“While some combinations did not achieve compatibilization, others materials were successful and became resin ingredients. As all these materials had an adverse effect on the physical properties necessary to ensure impact resistance, heat resistance, and other performance requirements, however, we were faced with a trade-off between weight-reduction and functionality. We were unable to satisfy the client’s requirements,” says the employee.
The team decided to increase the number of materials used and run a huge number of mixing tests involving a large variety of combinations.
However, all tests either failed to achieve compatibilization, or did not create significant points of difference with existing materials. No matter how many times the team tried, they could not come up with a resin that satisfied the clients requirements. Time ticked on with no progress being made.
Summary of the Problem
- The team experimented with various combinations of materials and compatibilizers but some combinations were unsuccessful.
- To reduce weight, the team needed to sacrifice the physical properties that ensured impact resistance and heat resistance.
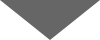